- PR & Content
- Strategy
Five manufacturing trends you can’t afford to ignore.
Our Senior PR and Content Manager, Ricco Leung, discusses five manufacturing trends we should take note of.
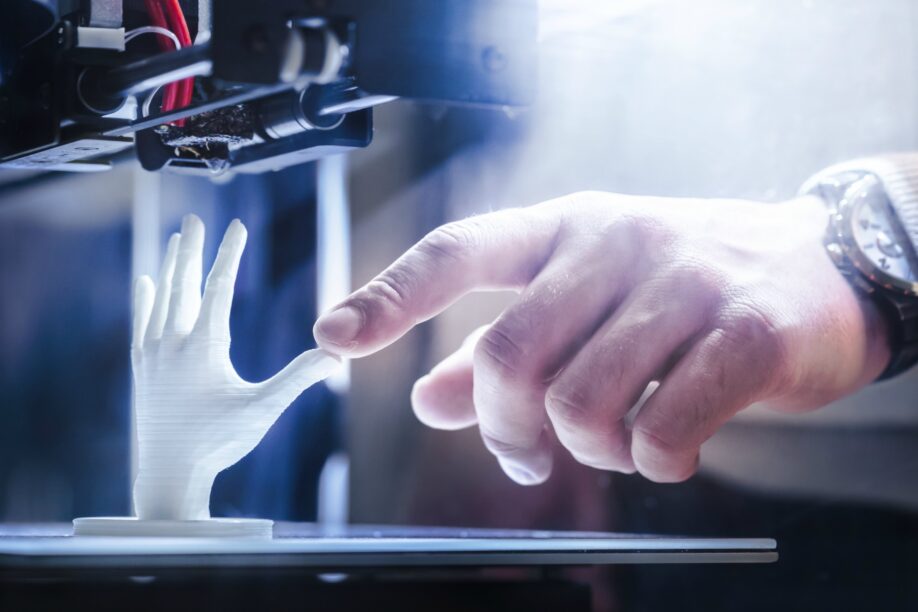
“Unglamorous, dull, dying-out.” …just some of the words the everyday layman might associate with manufacturing.
But how wrong they are.
Look deeper into manufacturing, and you’ll see that this industry is much more than just moving things along a production line in a sweatshop environment. Skills needed for the trade include planning out capital expenditure and investment on the factory floor, continuous improvement to make processes and machinery ever more efficient, ensuring the health and safety of staff, along with much more. Detail is everything.
The industry is evolving at a quicker pace than ever before too, with technology changing age-old methods and shaking things up. In the cut-throat world of manufacturing, if you don’t improve and adapt, you’ll soon become obsolete.
To that end, here are five manufacturing trends that you simply can’t afford to ignore:
1. Automation and IIOT – The biggest change to manufacturing since steam engines.
At the forefront of these trends is that of digitalisation. In the face of global competition and rapidly-shifting consumer trends, manufacturers are operating in uncertain and unpredictable environments.
Industry 4.0, automation, smart manufacturing – no matter how it’s referred to, the evolution of manufacturing is now well underway. While some manufacturers have been adopting smart technologies for several years, others are only just getting started, but – what’s certain – is that every manufacturer embracing the digital future is beginning to feel the benefits.
Those benefits have been well versed in the media, from automated processes through to data harnessing. What this means in reality is that factories can operate more:
- Efficiently
- Enhance production quality
- Minimise downtime
- Increase flexibility
The common question that comes about as a result of these benefits, however, is where humans fit into the future of manufacturing. The good news is that, as part of the digital evolution, people still have a part to play. Their roles will change, but through upskilling, people will still be needed.
2. With absolute accuracy – Metrology in manufacturing.

Metrology, otherwise known as the science of measurement, is an essential part of engineering and manufacturing. Having accuracy in measurement and recording allows for increased efficiency, saving time, money and improving technology along the way. With increased pressure on the need for low-run, individualised or even one-off units, having accurate and multiple methods of measurements are important for manufacturers whose machines may be required to utilise many different settings. Using the latest in metrology allows manufactures to take the next step in technology.
There has been a huge focus on metrology lately, with emphasis on the benefits of undertaking investment in metrology within manufacturing and how, when used in conjunction with non-destructive testing, metrology has the capability to monitor and inspect in greater detail, enhancing product quality and engineering to the next level.
Metrology has great applications across multiple manufacturing industries, including aerospace, motorsport, rail, marine and defence. There are multiple dedicated metrology centres in the UK, allowing manufacturers of any size to get access to the latest in measurement technology.
3. Flexible factories are the future.
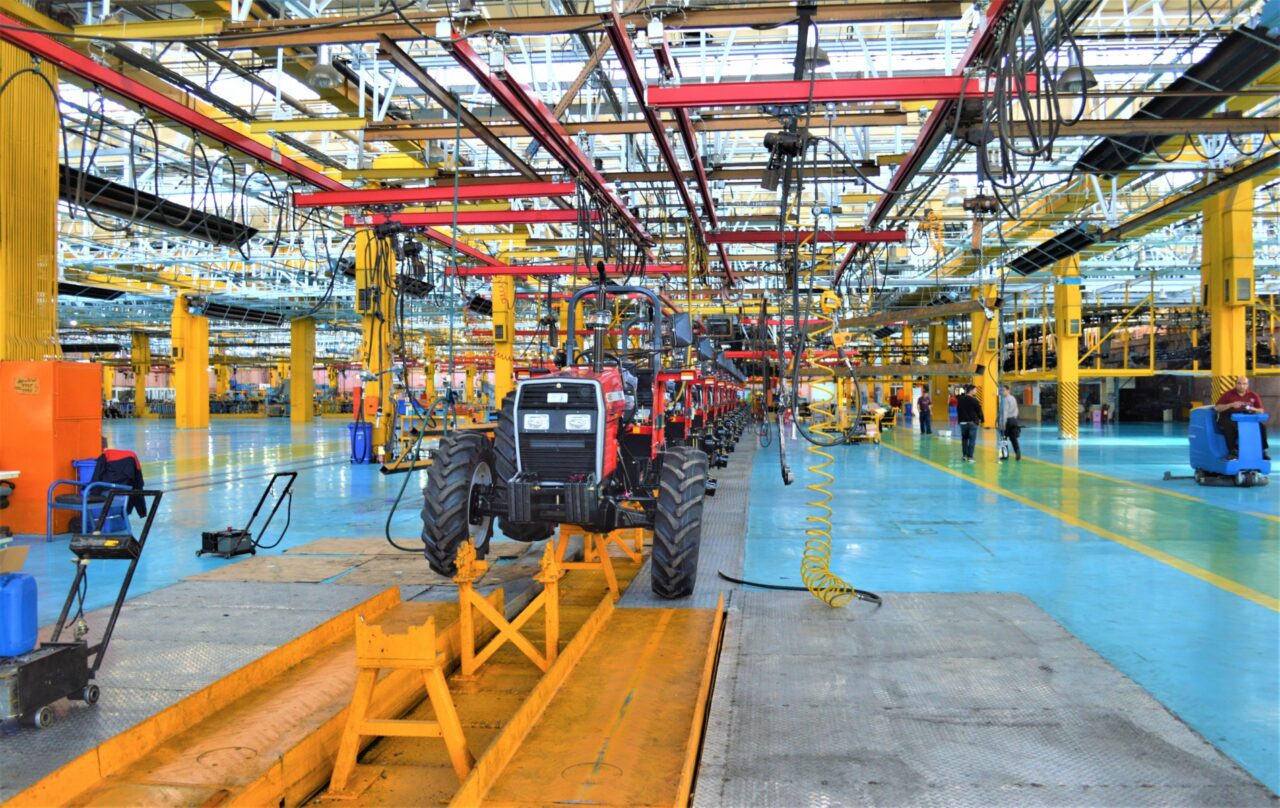
We already hear you asking, ‘What is a flexible factory and why are they needed?’
To answer the latter first, consumers are increasingly interested in customisation while manufacturers are keen to offer more choice. With customisation though comes longer waiting times. A great example is the automotive market, as a leading car review website found that the average factory order time for a new car is 13 weeks, while some could take up to 52 weeks.
Flexible factories overcome these issues, as they are designed in a way that they can be reconfigured – with minimum downtime – to produce a variety of similar products or tasks. This makes them much more responsive to customers, and greatly reduces supply-chain complexity.
This flexibility allows the factory to direct its efforts towards higher value engineering and manufacturing that can be undertaken in small to medium sized plants, minimising outlay for big plants with multiple production lines.
4. Living in a material world – The need for advanced materials.
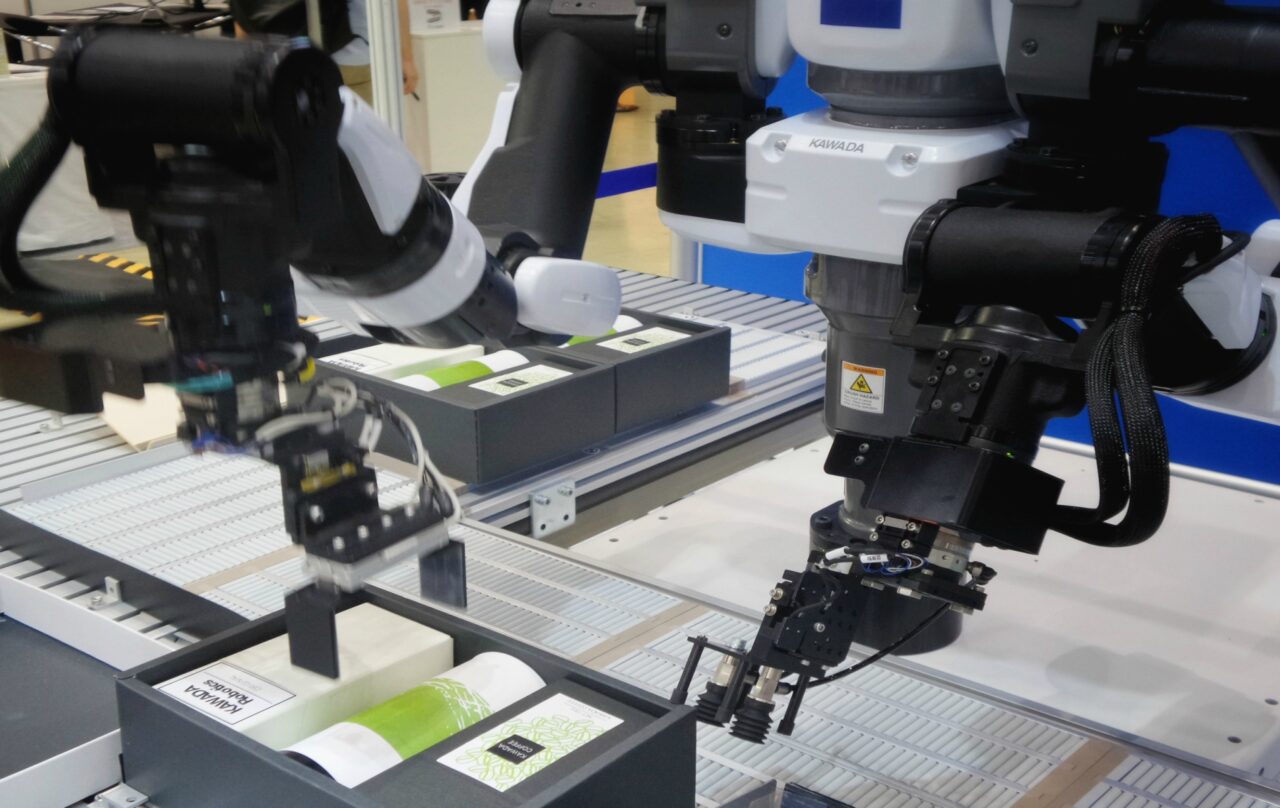
The success of manufacturing won’t just hinge on mechanics and machinery. The continuous research into advanced materials will certainly have their part to play as well.
Ceramics are a clear example. These human-engineered materials are being combined with additive manufacturing (3D printing) and are changing how engineers think about CAD and design. Prototypes are much easier and more cost effective to create than ever before.
"Thermal insulation materials are crucial to the future of manufacturing."
For example, these materials wrap around lithium-ion batteries to protect them from overheating and causing ‘thermal runaway’ fires. Engineers will have to look at how they can work with advanced materials manufacturers to create true innovation together.
5. 3D Printing and CLIP – Unlocking mass customisation.
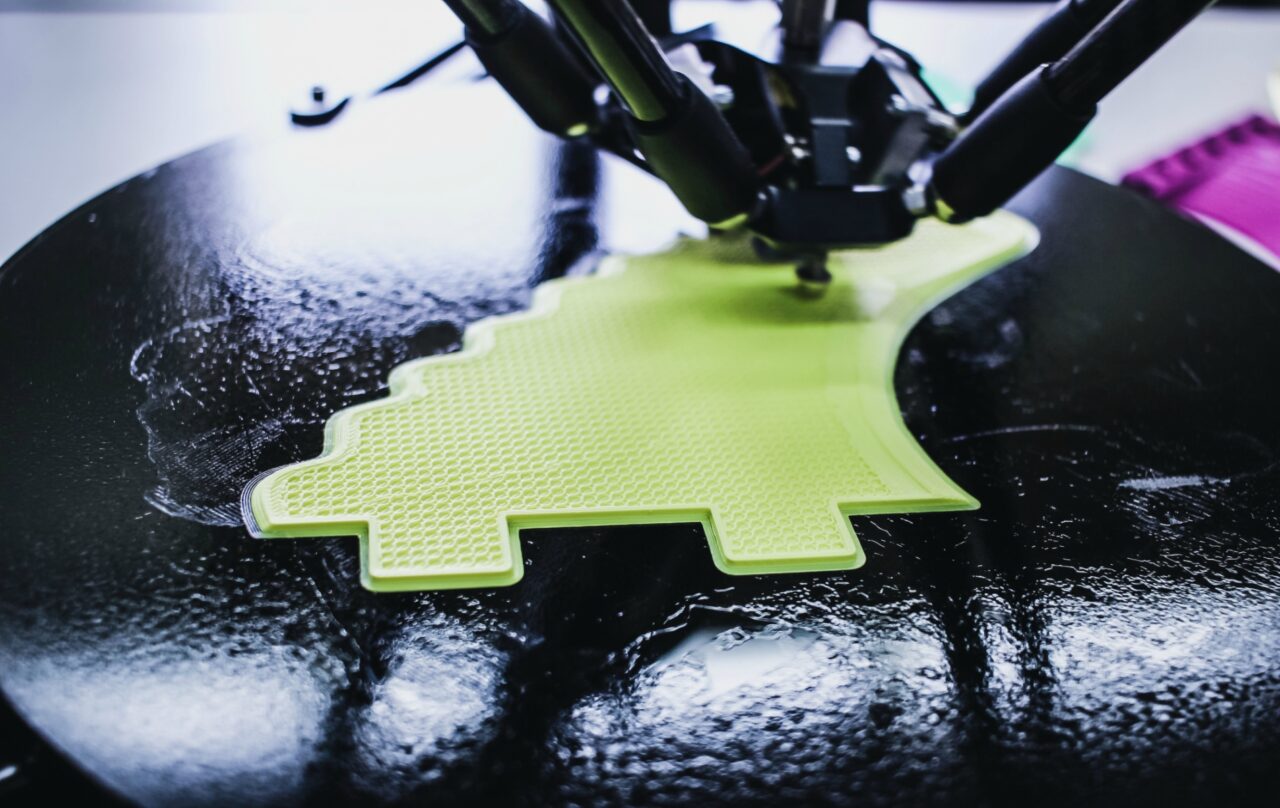
By now, most of us have heard of 3D printing (or additive manufacturing), if not, where have you been?
In layman’s terms, 3D printing is when 3D solid objects are made from a model on a computer. 3D printing is done by building up the object layer by layer. Usually, 3D printers use plastic and resin, because it is easy to use and cheap.
This manufacturing method has been around for a few years now and is generally used for producing small things like models and prototypes. However, it has now advanced to being able to create concrete, metal, ceramic and titanium products, such as handguns, components in healthcare machines, and even houses. Parts that were previously cost-prohibitive or even impossible to manufacture are now possible.
Additive manufacturing has disrupted how manufacturing works, but even this new method is being disrupted. CLIP (Continuous Liquid Interface Production) is a new form of 3D printing that is layer-free and enables objects to be printed 100 times faster than traditional additive manufacturing. This is creating new business opportunities such as mass customisation, on-demand inventory and differentiated products.
How we can help you get ahead in manufacturing.
With so much going on in the world of manufacturing, it can be hard to keep up with the trends and know how to plan where your company and brand is going.
However, standing still is not an option. Much like how manufacturers are challenging boundaries every day to seek improvement, we too at Wyatt look at how we can improve brand and business performance, whether that’s through PR and content marketing, B2B marketing strategy, lead generation or B2B social media or otherwise.
With over 55 years of working with some of the largest B2B brands in the world, many of whom are leading manufacturers in their field, we can help you tackle these trends head on.
Looking to become a thought leader in this new era of manufacturing? Contact us or email hello@wyattinternational.com